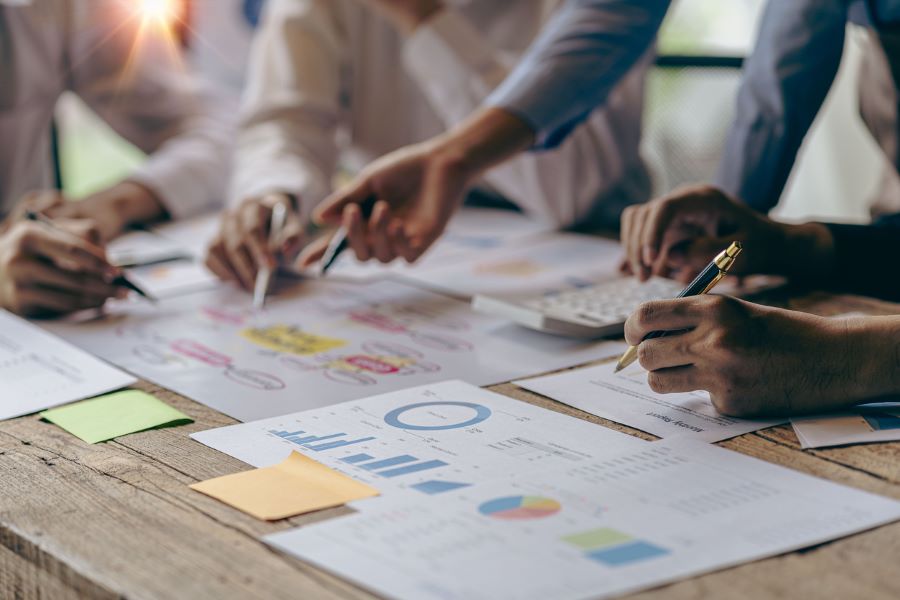
At TLScontact, our government clients want to be sure that we consistently provide visa application services according to the highest standards, everywhere, every time. And we must.
Our fundamental approach to achieving this global consistency is Lean management, a system that has its origins in post-war Japanese car manufacturing. This involves standardisation, rigorous problem-solving and accurate, timely data to monitor performance and drive decision-making.
Processes and quality standards are typically included in the standard operating procedures (SOPs) we agree on with the governments that depend on our services. For several years we’ve used the Lean approach to keep our promises, fostering a culture of continuous improvement across our operations and empowering our staff to contribute to these efforts.
Lean management at TLScontact involves three primary pillars:
Standard activities for managers
Leader Standard Work sets out standard activities for managers on a daily, weekly and monthly basis, creating a stable and productive work environment. It establishes regular schedules for routine tasks and helps leaders with decision-making thanks to access to timely, accurate data.
It also encourages regular, structured interactions between managers and their teams, through “huddle meetings” and one-to-one coaching for individual team members. “Gemba walks” (from the Japanese for “the actual place”) also allow leaders to check processes where they are done, and identify issues for resolution.
We use Leader Standard Work to embed best practices among our centre managers and promote organisation-wide consistency, complete with a dedicated online resource platform, as well as day-to-day support and coaching by our continuous improvement team.
Proven problem-solving
Lean management encourages a systemic approach to problem-solving, looking at the root cause of any issues to understand why they are occurring and how processes need to change to avoid them recurring.
A key element embedded across our organisation is the A3 problem-solving methodology. It establishes a problem statement and then follows a rigorous, eight-step process to analyse the issue, identify potential solutions and test them. The ultimate objective is to develop “built-in” quality, where employees get things right first time.
Real-time performance data
Timely, accurate data is at the heart of the Lean management approach: it provides the evidence and insights needed to identify waste, measure performance and drive continuous improvement. Without data, decisions are simply based on intuition or guesswork.
At TLScontact, we have dashboards in place for each of our centres, measuring key metrics such as productivity and customer waiting times. This allows our centre managers to focus on improving performance, making adjustments and testing how effective any changes are, in real time.
Entrusting their visa application processes to TLScontact is no small matter for the governments we serve. In turn, consistently getting it right and always striving to do better is no small thing for us – and we can achieve that with the correct approach: the Lean one.
Article written by Greg Lane,
Chief Transformation Officer